Strain testing allows both static and dynamic loads to be evaluated and can be used to troubleshoot existing systems to identify when there may be problems. When a structure has failed, strain testing can guide the detailed evaluation to determine the loading conditions that led to the failure. Strain testing allows the true environment to be identified to assess whether fatigue or overload conditions exist. Coupled with finite element analysis, strain testing allows thorough structural assessment for design validation. ATA is expert at conducting strain testing on existing structures at remote locations in the field.
Proof load testing is conducted to ensure that static or pseudo-static design loads can be handled by a structure. When these proof loads are applied, strain measurements are key to validating that the stress and load distribution in the structure are as expected and there are no unexpected hot-spots. ATA is expert at installing strain gages as and using finite element models (FEMs) to identify the critical locations where strain measurements are the most effective. ATA can provide assistance in the instrumentation installation process as well as signal conditioning and strain data collection and stress level monitoring.
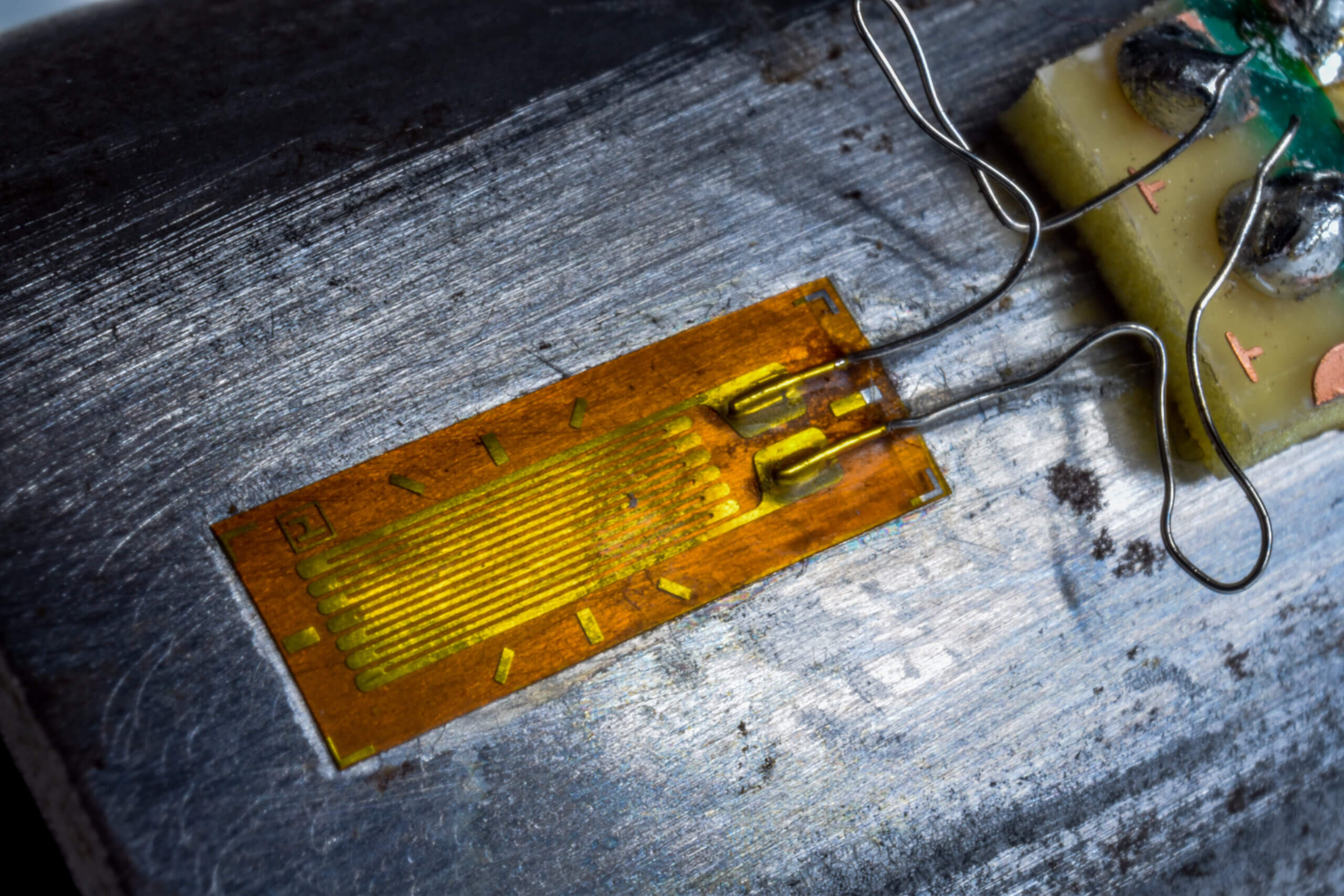
Dynamic stresses occur in all structures exposed to operational conditions. Dynamic strain measurements are key to identifying those dynamic conditions and determining whether they pose a risk to the structure. Fatigue and durability must be assessed to ensure that design life criteria are met. ATA has a long history of installing strain gages to monitor structural stresses during dynamic operating conditions. Our data acquisition equipment is tailored to allow simultaneous collection of multiple instrumentation parameters that can be used to evaluate structural integrity and fatigue life. The measurements listed here couple with the strain measurements to collectively allow clearer evaluation of the dynamic environment that the structure is exposed to and determine how dynamic loading affects the structural performance.
- Strain
- Load/pressure/acoustics
- Speed/tachometer
- Acceleration
- Displacement
- Temperature
ATA engineers are dynamics specialists with the experience to conduct dynamic strain testing using sophisticated instrumentation to provide a clear picture of structural responses and performance.
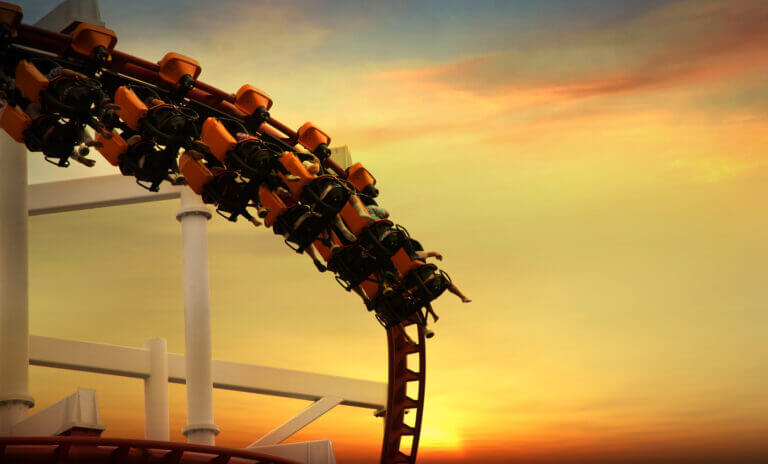
Strain gages, when properly installed, can be used as load sensors on existing structures. Load measurements are often desired on structures where it is difficult or impossible to install a load cell for the desired measurements. Arrays of strain gages can be used to provide independent load measurements when they are properly distributed.
ATA has developed methods for measuring structural operating loads based on strain readings and a series of strain-to-load calibrations. Using the test-measured strain-based loads and detailed FEMs, we can then provide our customers with accurate fatigue life predictions on components or in areas where strain readings are impossible to obtain. ATA has conducted numerous test programs on vehicles and other structures using strain gage arrays that can be combined in an independent manner to yield the desired load conditions. Independent loads are applied to the structure while strain arrays are monitored to develop the needed strain transformation matrix to be applied to the strain measurements. Once the strain measurements are made, the data is processed to yield the desired operating loads.
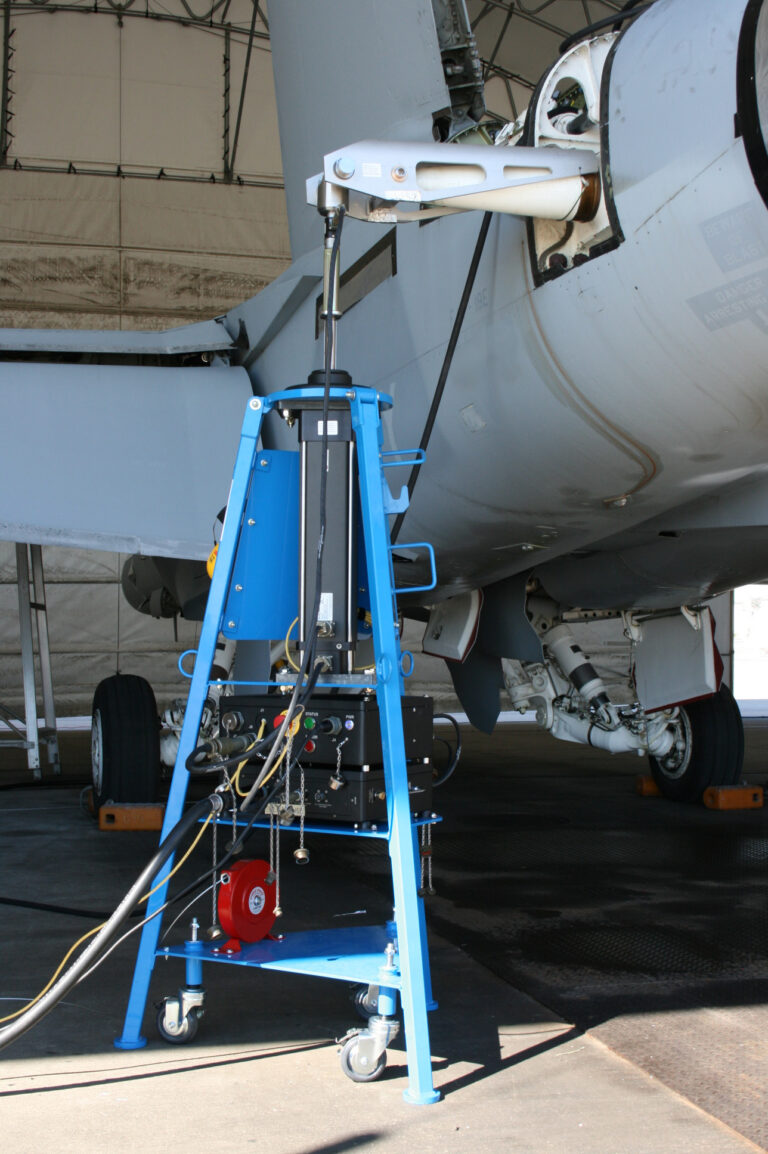
ATA is equipped with multiple strain conditioning and acquisition systems capable of providing quality test results in a variety of environments. Testing outdoors at our customer’s field site is a typical environment for our strain data acquisition systems. Our hardware is specifically designed for environments ranging from temperature-controlled lab conditions to extreme locations where temperature, moisture, vibration, dirt, and oil would damage or destroy other systems.
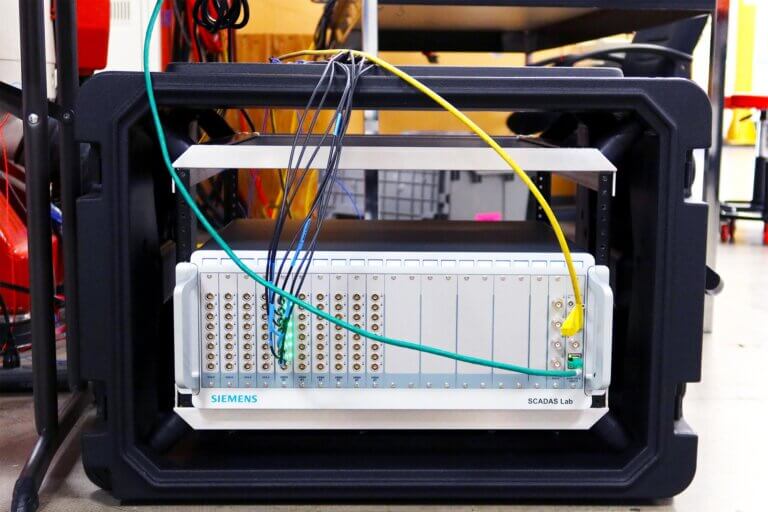
FEATURED Technical Paper
Analysis and Test Validation to Develop Mars Science Laboratory EDL Loads – Mobility Deploy Event
FEATURED Technical Paper
Direct Operational Loads Monitoring Approach for Structural Prognosis
FEATURED Technical Paper
Trained Network Force Measurement Approach for Aircraft/Store Interfaces
Connect with us to discuss how our advanced multi-disciplinary team can help you achieve your engineering goals.