ATA has proudly provided these test services for over 45 years, having pioneered numerous technical capabilities including random excitation, multishaker testing, orthogonal polynomial data processing, and automated test setup processes. Our advancements, such as our patented Multi-Sine sweep excitation (U.S. Pat. No. 8,281,659), Orthogonal Polynomial (OPoly) parameter estimation technique, and fixed base correction (FBC) technique, demonstrate our commitment to constant innovation of modal test methods. Our ability to deploy over 1000 channels of instrumentation and data acquisition equipment allows us to complete modal surveys of any size structure. We specialize in aerospace structures (e.g., aircraft, space launch vehicles, rocket motors, and satellites), but ATA can test virtually any dynamic system. As part of an aircraft GVT, often a structural mode interaction (SMI) test or ground resonant test (GRT) is performed. Instead of electrodynamic shakers exciting the aircraft, the aircraft control surfaces excite the structure. ATA can record the modal instrumentation set during SMI testing to achieve a large channel count measurement set for analysis.
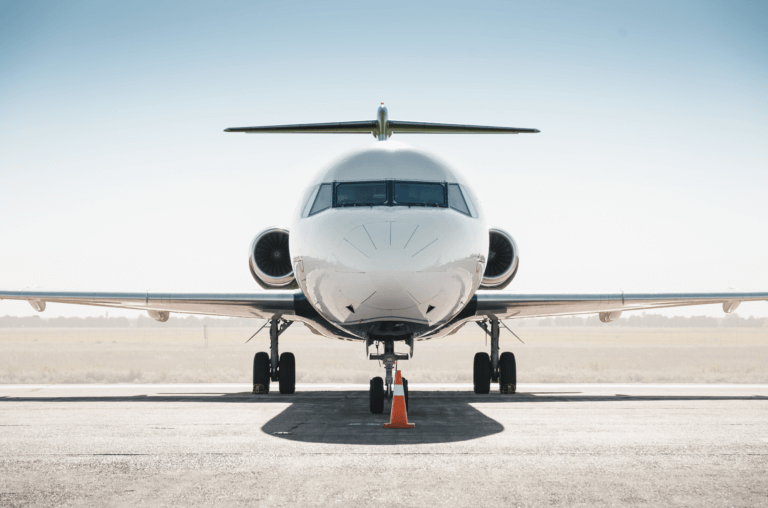
The full modal test process involves pretest planning, test performance, and posttest model updating and correlation. ATA is well versed in accomplishing all phases of the modal test process. Planning involves properly selecting measurement and excitation locations along with identifying which modes are of primary interest for the test article. This process is integrated with the finite element modeling activity and requires a tight integration between analysis and test efforts for the highest likelihood of success. ATA is an expert at conducting this pretest analysis process and developing all necessary planning documents that lead to test success. Use of the finite element model (FEM) in developing a test–analysis model (TAM) ensures tight integration between modeling and test activity throughout.
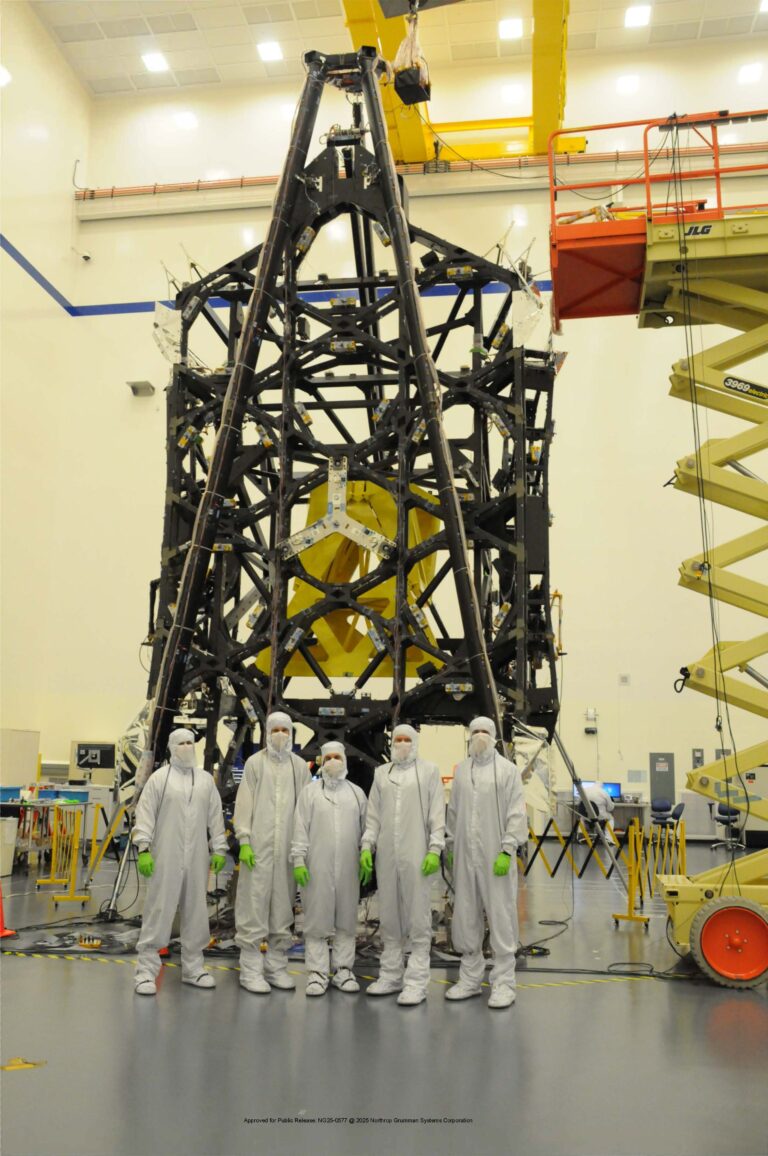
Familiarity with the preparation processes ensures that the proper steps are followed when conducting the test so that high-quality modal test data is obtained. ATA has implemented numerous tools to assess data quality and verify that all results fulfill the test objectives. Excitation methods are not limited to a single type, as the best results are achieved through implementation of a variety of techniques. Parameter extraction while testing is ongoing ensures that all test objectives are met and that modal results are obtained before the test is finished. When needed, additional data collection with variations in excitation locations or excitation techniques can be applied along with supplemental measurements. All results are verified before removing the instrumentation to confirm that there are no missing pieces of information that could necessitate costly test repetition.
ATA’s skill in preparing for and conducting the test contributes to our expertise in the posttest evaluation and model correlation process, as familiarity with the hardware generally leads to a better understanding of where model improvements can be made. Our test engineers are experts at both completing the testing program and conducting or assisting in the FEM updating process. This knowledge and cross-disciplinary skill ensure that the test results are well suited for making model improvements and that our test engineers have a better understanding when working with analysis engineers in the process.
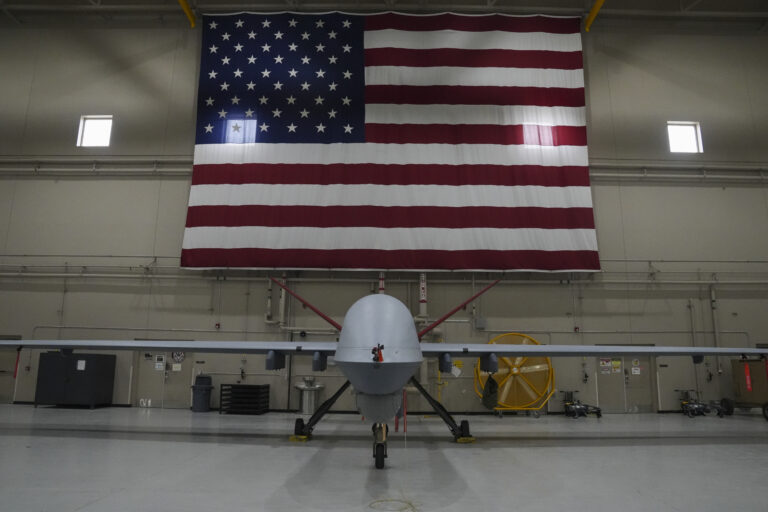
ATA owns a large inventory of test equipment that is tailored to preparation for and performance of large-scale modal tests. Our equipment includes a wide variety of accelerometers, shakers, impact hammers, scanning laser vibrometer, and data acquisition equipment, all of which are optimized for completing modal tests efficiently. Our equipment is transportable, which allows testing to take place conveniently at our customer’s site. Testing can also be performed at ATA’s facility; we have a 2200 square foot test facility with two T-slot tables for fixturing test articles, along with various handling hardware to accommodate a variety of modest-sized test articles.
ATA also offers equipment rental and expert consulting to facilitate our customers conducting their own testing activity.
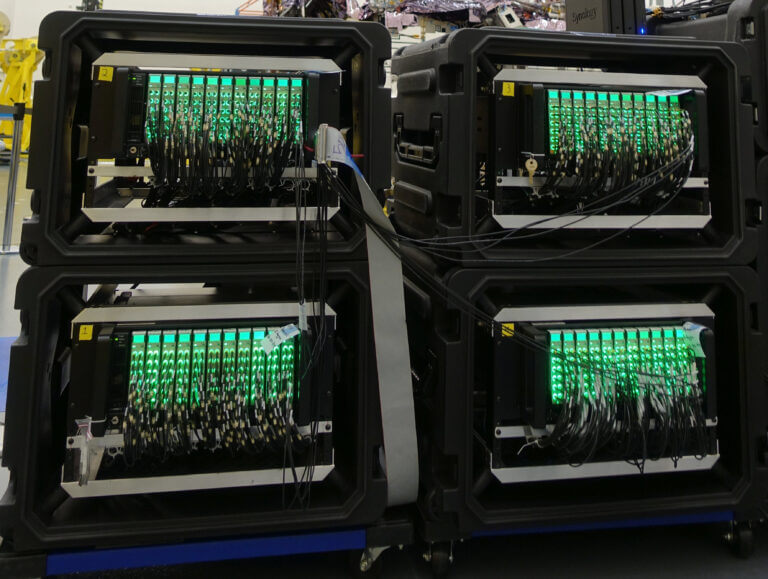
Oversight during testing performance is sometimes needed when personnel are just learning to conduct modal testing or learning how to use new test equipment. ATA can provide personnel, with supplemental test equipment, to provide oversight of test performance and help with the entire modal test process. We can review test plans and assist with other customer requirements. Being on site during testing enables immediate data review and recommendations for test adjustments, such as when shaker placement moves or instrumentation changes may be warranted. ATA’s expert advice can help ensure that modal testing is completed successfully.

A fixed base modal test is often desired but difficult to achieve. This challenge is common in the aerospace satellite industry, when testing and schedule constraints make it desirable to obtain modal data with a test article installed on a qualification shake table. Unfortunately, in most cases the flexibility and dynamics of the shaker and shake table do not provide the type of fixed base boundary condition desired, yielding unsatisfactory modal data. It would be ideal if a high-quality fixed base modal survey could be performed with the test article mounted on a shaker table. ATA has developed and implemented the FBC modal test technique, which provides fixed base modes while a test article is mounted to a dynamically active base such as shaker tables and static test fixtures. This approach allows for a substantial reduction in the overall development process time while still achieving the desired test conditions for model correlation.
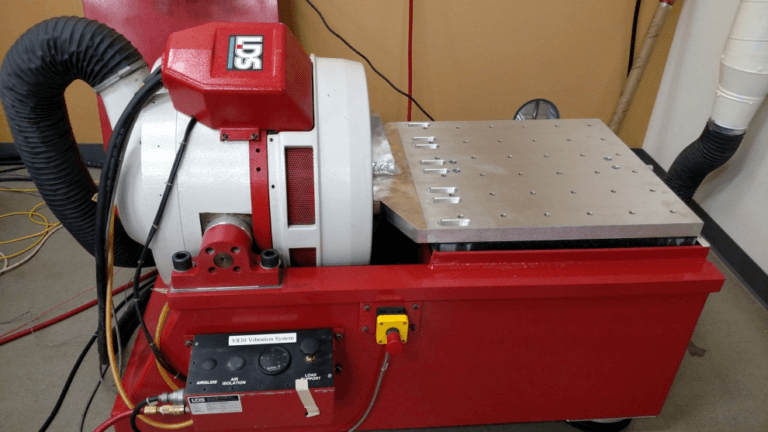
A free-free boundary condition for modal testing and GVTs is often desired but difficult to achieve. This challenge is common in the aerospace industry; when testing aircraft, it is desirable to obtain modal data with a low-frequency isolation system to simulate a free-free boundary condition. For these circumstances, ATA has developed and implemented several variations of isolation systems using bungees. The variations include both overhead and below-gear systems. The overhead method, which is practical if overhead lifting capacity is available, can utilize pickup points on the aircraft or web slings to support the aircraft. Below-gear systems utilize a welded steel structure, jack screws, and bungees to roll the aircraft onto a custom platform and then activate a lifting mechanism to engage the bungees to float the aircraft. Let us help you with your custom solution.

Certain test articles require noncontact modal testing to minimize test setup effects, including shaker-structure interactions and mass loading, which alter the dynamics of the unit under test and increase uncertainty in the data. To minimize uncertainty in your data, ATA has a full complement of noncontact modal testing equipment to test even the smallest and most delicate test articles. ATA has successfully utilized our scanning laser vibrometer, automatic impact hammers, acoustic arrays, and acoustic excitation sources on a variety of structures ranging from sporting equipment to printed circuit boards and small turbine blades. Let us help you identify the optimal noncontact modal test setup for your specific application.
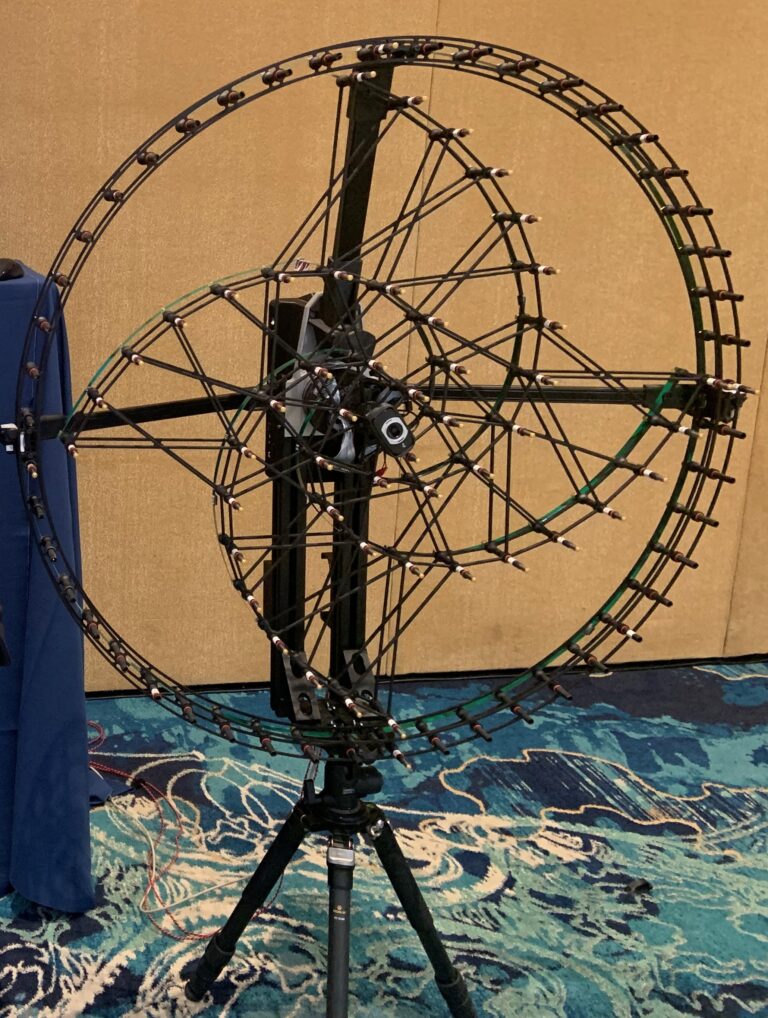
FEATURED Case Studies
Analysis and Testing of the Predator UAV
General Atomics Aeronautical Systems, Inc., (GA-ASI) develops and manufactures the Predator line of aircraft, a highly successful long-endurance remotely piloted aircraft (RPA) used in surveillance and reconnaissance missions around the globe. ATA Engineering, Inc., has supported GA-ASI by modeling, analyzing, and testing different variants of the Predator.
FEATURED Case Studies
Complete GVT of the 747 SP SOFIA Aircraft
A Boeing 747SP aircraft was modified by L-3 Communications Integrated Systems to accommodate a 2.5 meter reflecting telescope as part of the SOFIA program. SOFIA, the largest airborne observatory in the world, is a collaborative effort of NASA and DLR, the German Aerospace Center.
FEATURED Case Studies
Ground Vibration Test and Structural Mode Interaction Assessment of an Aircraft
Tamarack Aerospace Group (Tamarack) does airplane modifications. In this project, Tamarack retrofitted specialized winglets, with active camber surfaces, to an existing airplane. That modification requires EASA and FAA certification of the aircraft.
Connect with us to discuss how our advanced multi-disciplinary team can help you achieve your engineering goals.